以某家涂料生产企业为例,分析大风量、低浓度非连续排放有机废气治理技术的经济性。结果发现:(1)对于大风量、低浓度有机废气,在几种主流治理技术中,当回收液具有利用价值时,"活性炭吸附-氮气脱附冷凝溶剂回收技术"相较"RTO(蓄热式热氧化)技术"、"沸石转轮吸附浓缩-RTO技术"及"沸石转轮吸附浓缩-CO(催化氧化)技术"的经济性更优;而回收液需作为危废处置时,"沸石转轮吸附浓缩-CO技术"更具经济性,但必须考虑来气的情况,选择合适的催化剂,确保系统运行的稳定性。(2)对于非连续排放的废气,"分散收集,集中处理"的治理模式有利于降低VOCs治理装置投资成本,具有很好的经济性。
挥发性有机物( VOCs) 作为光化学反应的重要前体物,是产生灰霾的主要根源,不仅危害环境而且危害人类健康,近年来受到社会高度重视,VOCs治理迅速掀起了一股热潮。
VOCs治理技术有吸附、冷凝、吸收、膜分离等回收技术,以及燃烧、生物、低温等离子体、紫外光催化氧化等消除技术,以及根据废气特点采取组合技术。近年来,对于大风量、低浓度有机废气,治理的主流技术有“RTO ( 蓄热式热氧化) 技术”“沸石转轮吸附浓缩- RTO 技术”“活性炭吸附- 氮气脱附冷凝溶剂回收技术”和“吸附浓缩- CO ( 催化氧化) 技术”,广泛运用于汽车涂装废气、家具厂喷漆废气、包装印刷废气、涂料生产废气等的治理。
企业在选择VOCs 治理技术时,必须兼顾技术可行性和经济适宜性,昂贵的投资和较高的运行费用对于很多企业来说难以承受。涂料生产废气是典型的大风量、低浓度有机废气,因此,本文以非连续生产的某涂料生产企业为例,比较几种可行技术方案的经济性,为优化VOCs 治理方案提供参考。
1 VOCs治理技术经济性分析
1. 1 各技术工艺简介
1. 1. 1 RTO技术
RTO 是一种配有蓄热床层的热力燃烧治理技术,蓄热燃烧系统主要由燃烧装置、蓄热室( 内有蓄热体) 、换向系统、排烟系统和连接管道等组成( 见图1) ,其工作原理为: 将有机废气加热至750℃以上,使废气中的有机物氧化分解成CO2和H2O,氧化反应产生的高温气体流经蓄热体,使蓄热体升温而“蓄热”,进而用于预热后续进入的有机废气而“放热”,从而节省废气升温所消耗的燃料量,蓄热体“放热”后立即引入适量洁净空气进行清扫,待清扫完成后才能进入“蓄热”程序。三室RTO 是目前主流的应用装置,蓄热体分为三个室,每个室依次经历“蓄热—放热—清扫”等程序,如此反复。由于蓄热系统的热回收效率很高,该技术可对具有一定浓度的连续排放的有机气体进行高效且较经济的处理。
1. 1. 2 催化氧化技术
催化氧化系通过催化剂的作用减低挥发性有机物的氧化反应所需的温度,与直接燃烧相比,由于燃烧温度较低,对设备材料和保温的要求相应减低,同时排气温度通常也低于直接燃烧,达到一定的节能效果,总体占地面积小,风量不大时投资相对较小。催化氧化工艺流程见图2,催化工艺在选择催化剂时需要全面考虑来气的情况,确保催化剂在使用过程中不出现失活现象才能达到设计的性能和催化剂使用寿命。由于采用的是间壁式换热装置,其热回收率要大大低于RTO。
1. 1. 3 沸石转轮吸附浓缩-RTO ( 或CO) 技术
该技术是沸石转轮吸附同RTO ( 或CO) 技术的组合工艺,系统主要由粉尘过滤器、沸石转轮浓缩吸附装置、RTO ( 或CO) 、风机、换热器、PLC自动化控制系统等组成( 见图3) 。该组合技术通过沸石转轮的吸附浓缩使大风量、低浓度有机废气浓缩为较小风量的高浓度气体,高浓度气体再经RTO 或CO 高温氧化分解为CO2和H2O。转轮的工作原理为: 转轮以一定转速连续旋转,转过吸附区、脱附区和冷却区,有机废气在吸附区被吸附净化,吸附在转轮中的有机物在脱附区被热风脱附浓缩后进入RTO 或CO,脱附后的转轮转到冷却区被冷却,再旋转至吸附区,持续吸附VOCs 废气,周而复始,连续工作。
1. 1. 4 活性炭吸附- 氮气脱附冷凝溶剂回收技术
该技术是活性炭吸附与冷凝的组合工艺,系统主要由粉尘过滤器、颗粒活性炭吸附装置、氮气脱附系统、风机、冷凝系统、PLC 自动化控制系统等组成( 见图4) 。该组合技术通过活性炭吸附- 高温氮气脱附使大风量、低浓度有机废气浓缩为高浓度气体,高浓度气体再经冷凝系统冷凝成溶剂并回收。脱附再生后的活性炭再继续用于VOCs 废气的吸附。
1. 2 案例的技术经济性分析比较
根据某涂料生产企业废气的排放情况,采用以上主流工艺设计若干可行的技术方案,并通过各技术方案的投资和运行费用等分析比较,从技术经济性角度进行方案优选。
样本企业VOCs 废气情况: 废气排口有5 个,三个车间,车间排口数分别为2 个、2 个、1 个,由于涂料生产的特点,排放VOCs 气体的浓度不稳定,约100 ~ 400mg /m3。该企业每周生产5d,每天生产8h,VOCs 废气具有大风量、低浓度、非连续稳定排放的特点。
结合废气污染源的情况,设计了7 种备选方案,如下:
方案A 配置5 套处理能力25 000m3 /h 的RTO;
方案B 配置5 套处理能力25 000m3 /h 的转轮浓缩加3 000m3 /h 的RTO;
方案C 配置2 套处理能力50 000m3 /h 的转轮浓缩加5 000m3 /h 的RTO,1 套处理能力25 000m3 /h 的转轮浓缩加3 000m3 /h 的RTO;
方案D 配置5 套处理能力25 000m3 /h 的活性炭吸附- 氮气脱附冷凝溶剂回收装置;
方案E 配置2 套处理能力50 000m3 /h 的活性炭吸附- 氮气脱附冷凝溶剂回收装置,1 套处理能力25 000m3 /h 的活性炭吸附- 氮气脱附冷凝溶剂回收装置;
方案F 配置5 套处理能力25 000m3 /h 的转轮浓缩加3 000m3 /h 的CO;
方案G 配置2 套处理能力50 000m3 /h 的转轮浓缩加5 000m3 /h 的CO,1 套处理能力25 000m3 /h 的转轮浓缩加3 000m3 /h 的CO。
考虑到生产为非连续性,按每天排放8h,平均排气浓度250mg /m3 考虑。方案A、B、C 中的RTO 每天启炉一次。方案B、C 中的转轮浓缩加RTO 系统正常运行时,由于增浓后的气体浓度达到RTO 自持氧化浓度范围,不考虑浓缩后气体的RTO 辅助燃料费用,仅考虑转轮浓缩的加热附加燃料费用。由于风量大浓度低且间歇运行,方案D、E 按每5d 保护作用时间的吸附容量设计,每套系统配备由两台并联吸附床构成的可就地再生吸附净化系统,生产扩产时可实现连续运行。方案F、G 的CO 也是每天启炉一次,但需要补充一定量的燃料以维持CO 的正常运行。
对于RTO 系统,其直接运行费用包括风机及辅助系统的电费、辅助燃料费( 包括启动加热和进气浓度不高时的辅助加热) 和运行维护人员费用。对于风量25 000m3 /h 的RTO,其装机功率按55 kW 计,进气浓度按平均250mg /m3 考虑; 对于5 000 m3 /h 的RTO,其装机功率按22kW 计,不考虑辅助燃料消耗; 对于3 000m3 /h 的RTO 的功率按12kW 计,也不考虑辅助燃料消耗。考虑到RTO系统每天的启动加热操作,每天运行按10h 计。由于是非连续运行,每台RTO 均考虑每天启动烘炉的燃气消耗,烘炉燃气量参照RTO 的供应商提供的数据估算。
对于25 000m3 /h 转轮浓缩系统,兼顾3 级预处理过滤的阻力及再生气体的动力等,主风机、辅助风机等功率按20kW 计; 50 000m3 /h 转轮浓缩系统,按35kW 计,由于进气浓度较低,均考虑了脱附加热所需的燃气消耗。
25 000m3 /h 活性炭吸附系统的吸附风机功率按22kW 计,每天按8h 运行时间计,再生系统装机功率75kW ( 含制冷系统) 。方案D 按平均每天再生一套、每次再生5h 设计,再生过程采用的高温氮气用蒸汽加热,再生耗蒸汽量每次按1. 5t 计。
方案E 为2 套50 000m3 /h 和1 套25 000m3 /h 的活性炭吸附加氮气脱附装置,3 套系统每周各再生1次,费用平均到5d 得到日运行费用。
对于CO 系统,其直接运行费用包括风机及辅助系统的电费、辅助燃料费( 包括启动加热和辅助加热) ,催化剂运行20 000h 后的更换费用和运行维护人员费用。对于5 000 m3 /h 的CO,其装机功率按5. 5kW 计,辅助燃料消耗按进出口温差140℃计; 对于3 000m3 /h 的CO 的功率按4kW 计,辅助燃料消耗按进出口温差140℃计。考虑到CO系统每天的启动加热操作,每天运行按8. 5h 计。由于是非连续运行,每台CO 均考虑每天启动烘炉的燃气消耗,烘炉燃气量按将催化床加热到300℃时的热量平衡数据估算。
由于RTO、转轮浓缩加RTO 以及转轮浓缩加CO 涉及的热氧化系统套数多,且需要每天启动时加热炉体,工作时间较长,需3 ~ 4 人运行。再生式活性炭系统,为全自动运行,尽管再生时需要值守,方案D、E 因采用的是就地再生,只需配备1人即可操作运行。电费按0. 8 元/kW·h 计,天然气按3. 5 元/m3 计,蒸汽按0. 3 元/kg 计,人员费用按300 元/d 计。
基于以上方案及基础数据,可得到不同方案的运行费用( 表1) 。表1 中系统的投资费用由于涉及到技术专利、材质、设备及自控元器件等配置的差异,结合供应商的询价,给出了大致的价格区间。
在表1 投资费用基础上取中间值,并按10 年使用寿命,5%的利率及每年工作250d,平均设计浓度250mg /m3,回收率90% 等条件计算出的年度直接费用、间接费用和年度总费用情况如表2 所示。其中活性炭方案D、E 分别给出了回收液回用( D1、E1) 和作为危废处置( D2、E2) 两种情况的费用,回收液可用价格取5 000 元/t,危废处理费按8 000 元/t 计。
方案A 对于低浓度且非连续排放的气体采用RTO 工艺,一方面RTO 的气流阻力较大,浓度低时需要添加辅助燃料,同时间歇运行,每天均需要进行启动升温,总体上非常不经济。
方案B 采用沸石转轮浓缩加RTO 的方式,由于浓缩系统的流体阻力较小,故有效地减少了主体气流的阻力,同时浓缩后的气体再进行热氧化减少了热氧化的辅助燃料需求,但每天的启炉和转轮的热再生需要消耗一定的动力能源。
方案C 系根据样本企业的实际情况进行的优化,通过合并系统的规模效应提高了技术经济性。
方案D 配置活性炭吸附氮气保护脱附系统,因吸附净化阻力不大,总体运行成本*低,由于活性炭系统的吸附能力,与热氧化系统相比更加适用于非连续排放过程,但因工艺复杂及安全配置的因素,投资费用不低。该系统主要用于溶剂回收,进口气体浓度高时,技术经济性更佳。对于样本企业,回收的溶剂可用于低端产品制造。因此D1 方案情景总体年度费用较热氧化方案具有优势。如表2所示,如果回收液无法利用,则还需要考虑将收集液体作为危废的处置的运行费用,如D2 方案情景所示,活性炭吸附氮气保护脱附系统的运行费用要超过浓缩热氧化系统。
方案E 为方案D 根据企业情况的优化版,通过合并系统的规模效应提高了总体的技术经济性。方案E1 情景在所有方案情景中总年度费用*低。
方案F 为沸石转轮浓缩加CO 的方式,与方案B 相比,由于CO 床层阻力较RTO 要小,所以总体电耗减低,但由于通常情况下催化燃烧的热回收率要远低于RTO,所以需要添加一部分辅助燃料,因此总体动力费用差距不大。但考虑到催化剂的更换费用,总体直接运行费用要高于RTO。CO 系统在小风量情况下的投资要小于RTO,因此总年度费用总体较低。但使用CO 设备时,在控制催化剂失活保证系统性能稳定性方面需要特别注意。
方案G 为方案F 根据企业情况的优化版,通过合并系统的规模效应提高了总体的技术经济性。
从表2 可知,对于样本企业,“RTO 技术”投资和运行费用*高,在回收液可以回用于生产时,“沸石转轮吸附浓缩- RTO 技术”及“沸石转轮吸附浓缩- CO 技术”投资和运行费用也明显高于“活性炭吸附- 氮气脱附冷凝溶剂回收技术”。所以,就样本企业的情况而言,从经济性角度,优先采用“活性炭吸附- 氮气脱附冷凝溶剂回收技术”,且方案E 优于方案D。
2 治理模式改进
2. 1 “分散收集,集中处理”模式
根据前述技术经济性分析,选用“活性炭吸附- 氮气脱附冷凝溶剂回收技术”对样本企业废气进行治理。
考虑到间歇排放且VOCs 排放负荷较低,为了进一步减少投资,同济大学提出“分散收集,集中处理”的区域范围VOCs 减排控制模式,即方案H,配置7 套( 5 用2 备) 处理能力25 000m3 /h 移动式活性炭吸附装置和1 套活性炭装置再生中心,该方案中“分散收集”指采用5 个移动式活性炭吸附装置分别对5 个排口VOCs 废气进行吸附净化,当吸附一段时间后,在线监控设施显示排口VOCs 浓度接近60% ~ 80% 的排放限值时,将移动式活性炭吸附装置运送到厂内集中建设的一套“氮气脱附冷凝溶剂回收系统”的活性炭装置再生中心进行脱附再生,同时排口处更换一个再生过的移动式活性炭吸附装置。
方案H 和方案D 规模和再生频次相似,只是方案H 需要进行吸附器的移动,活性炭吸附系统排气点处为吸附过程,无需人员运行看管。系统运行时,每天的主要工作为1 台吸附装置的更换移动及再生中心5h 的再生,系统的运行和维护按2 人计。方案H 的年度费用情况见表3,投资费用在500 ~ 700 万元之间,尽管人工费用有所增加,但总体年度费用仍然明显低于方案D、E。
方案H 主要针对间歇生产的特点,采用可移动式活性炭吸附装置加集中再生的模式进一步提高了技术经济性。由于生产装置运行前不需要特别提前对环保装置进行预热,集中再生可有效提高再生装置的使用效率,特别适合于大风量、低浓度非连续排放的污染源的控制。该模式突破了常见的活性炭吸附- 脱附一体化就地处理的模式,大大减少了建设造价。
该治理模式控制的关键是对废气排口VOCs 浓度进行实时监控,样本企业采用较经济且维护较简单、便捷,使用相对安全的光离子气体检测仪( PID) 进行内控监测。监测数据可以在手机应用程序上实时查看,一旦数据达到设定的监控上限值时,就更换移动式活性炭吸附装置。
2. 2 实际运行效果说明
方案H 实施后,为了验证该治理工艺的治理效果,样本企业委托第三方对5 个废气排口进行了监测,移动式活性炭吸附装置进出口非甲烷总烃的监测结果见表4,结果显示废气经治理后5 个排口非甲烷总烃均能达标排放,且在一定条件下,非甲烷总烃的去除效率能达90%以上。
方案H 实施后,样本企业的实际投资和运行费用与方案H 预期相差不大( 见表4) ,由于样本企业实际生产负荷低,产生的废气浓度低,且非连续稳定排放,日回收溶剂量为86. 2 kg,回收溶剂用于低端产品生产,可产生431 元/d 的经济效益( 见表5) 。
2. 3 移动式治理模式的应用前景
活性炭吸附技术是简单易行的治理技术,是一些分散的诸如喷涂、印刷、化工等小型企业首选的治理技术。但单个企业建设相应的活性炭再生系统费用高,小企业往往难以承担。如果采用更换活性炭的方式,新活性炭购买和废活性炭作为危废处置的费用均很高。因此,要减轻单个企业的治理费用,可采用移动式治理模式,将吸附饱和的活性炭,送到统一建设的活性炭异位( 地) 再生平台进行再生,大大减少单个企业的投资费用。也可采用“吸附- 移动脱附”的VOCs 净化技术,废气收集后经多级过滤装置去除漆雾、颗粒物,再经分子筛吸附床吸附后达标排放。吸附床吸附饱和后由移动式解吸装置原位脱附,脱附出的VOCs 经催化燃烧装置净化处理。
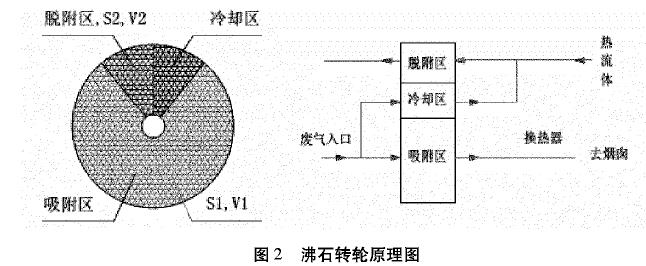
总之,无论是异位脱附还是原位脱附的移动式治理模式,都是打破传统的吸附- 脱附一体化模式,优化吸附剂再生方式,具有更好的经济性,尤其适用于非连续排放的废气。
3. 1 对于大风量、低浓度有机废气,在几种主流治理技术中,当回收液具有利用价值时,“活性炭吸附- 氮气脱附冷凝溶剂回收技术”相较“RTO”“沸石转轮吸附浓缩- RTO 技术”及“沸石转轮吸附浓缩- CO 技术”的经济性更优; 而回收液需作为危废处置时, “沸石转轮吸附浓缩- CO 技术”更具经济性,但必须考虑来气的情况,选择合适的催化剂,确保系统运行的稳定性。
3. 2 对于非连续排放的废气, “分散收集,集中处理”的治理模式有利于降低VOCs 治理装置投资成本,具有很好的经济性。
版权声明:本网注明来源为“环亚环保”的文字、图片内容,版权均属本站所有,如若转载,请注明本文出处:http://www.ythyhb.com 。同时本网转载内容仅为传播资讯,不代表本网观点。如涉及作品内容、版权和其它问题,请与本网站联系,我们将在及时删除内容。